How Our Branded Water Bottles are Made - Videos
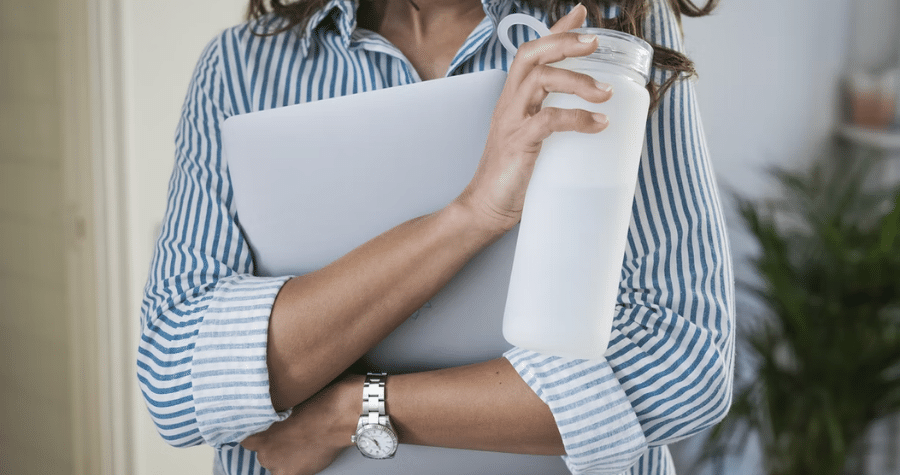
If you’ve never stopped to think how your branded products come into being, then what have you been thinking about?!
Here’s an insight into how one of our most popular water bottle designs goes from small plastic pellets to a functioning, screen printed bottle. And it all happens here in the UK.
Blow Moulding
Glassblowing was the inspiration for the science behind blow moulding which was first put into commercial use in the late 1930s when mass production of plastic bottles started in America, replacing some of the traditional glass bottles and packaging of the previous decades.
This video shows you the process called blow moulding in our modern
UK production facility; taking raw plastic to a beautifully formed bottle!
Step 1
The small plastic pellets are heated until they melt into a semi-liquid and can be ‘extruded’ into a tubular shape.
Step 2
The tube is then clamped within the bottle shaped mould.
Step 3
Moving a little along the production line, hot air is then blown into the plastic tube, forcing it to take the shape of the mould. The mould is then cooled and the newly shaped bottle is released.
Step 4
The excess plastic is then trimmed from the top of the bottle with a blade. Et voila, the bottle is ready for printing!
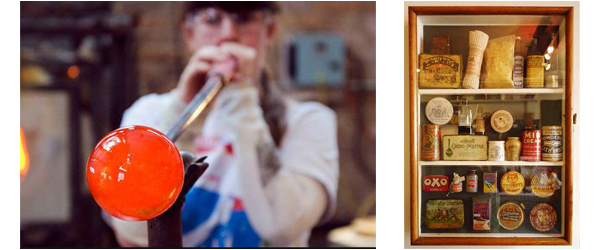
Glass Blowing inspired the process called Blow Moulding - first used commercially in the USA for packaging & bottles.
Screen Printing
Incredibly, screen printing in a recognisable form has been around since the 10th century, and the essence of the technique hasn’t changed. Take a look at our video showing how it’s now used for just one of thousands of branding applications in a more hi-tech production environment.
Step 1
Once lined up, each bottle is printed with ink which is forced through a mesh while the bottle turns beneath it. The mesh in the screen takes the 2D shape of the brand name or logo, allowing the ink to go through the mesh, printing the logo onto the bottle.
Step 2
A high intensity UV light is then used to ‘cure’ or harden the ink almost instantly so that the bottles can go to the next stage.
So there you have it...
The journey from plastic pellets to a branded water bottle! Many of our products use the blow moulding and screen printing processes, but dozens of other techniques are used to bring our customers the durable, stand-out products displaying the all-important promotional message for their organisation.
If you'd like to discuss how Fluid can help you and your brand with merchandise campaigns, don't hesitate to get in touch. Simply pop some details in the form below, we'll be in contact shortly!